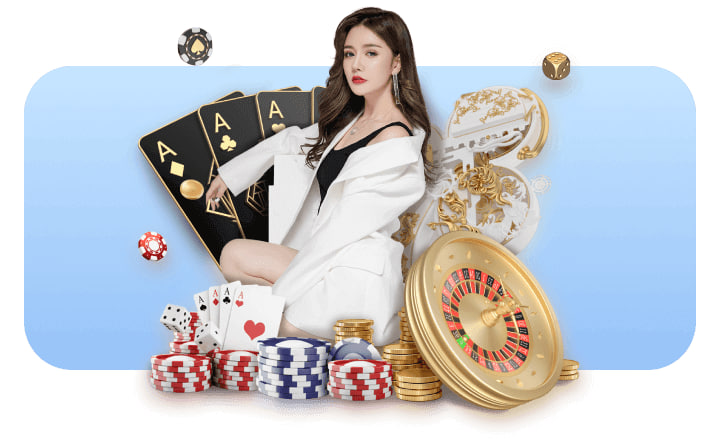
400-123-4657
点击量:582 时间:2024-01-24
澳门第一娱乐娱城官网中国涂料工业发展概况及水性化发展概况目前,我国涂料行业的产量和经济总量位居全球第一,是世界涂料大国。在过去的十年中涂料行业发展迅速, 增长喜人, 但是行业总体大而不强,发展方式粗放, 落后产能、过剩产能比较严重,产业集中度不高,涂料产量在地域上的分布也不均衡, 绿色环境友好型涂料占比较低且技术储备不足。特别是中央政府和各级地方政府近几年出台了诸多与涂料行业相关的环保和安全的政策法规,涂料行业在环保治理和安全生产方面面临十分严峻的挑战, 在种种挑战和压力下, 促进涂料、涂装企业寻找生存之道, 勇于且乐于转型升级,投资开发环境友好型涂料产品及涂装技术,设备的研发, 促进整个行业向中高端绿色环保方向发展。
虽然中国已经是全球最大的涂料生产国,但由于其涂料产业起步较晚,目前全球前十大涂料生产企业仍然集中在北美、欧洲及日本。到2009年,我国涂料克服了2008年以来全球金融危机的不利影响,总产量达755.44万吨,首次跃居世界第一。
中国工业化及城市化的进程为工业涂料、建筑涂料等快速发展提供了契机,涂料行业的技术水平进步较快,涂料的品种也日趋丰富和完善,涂料产销量也有了大幅的提升。中国油漆及涂料的销量由2010年的970万吨增至2018年的2100万吨,复合年增长率为10%,并预期于2022年达到2600万吨左右,显示2019年至2022年的复合年增长率为5%左右。[图表1-1]
中国涂料工业的市场容量前景广阔,下游的旺盛需求将维持涂料行业的增长势头。目前,中国涂料发展不均匀,在建筑涂料、家具涂料方面等已经可以自给自足,但较高档的汽车涂料、船舶涂料等则基本依赖外资品牌或者进口。从细分市场产量来看,建筑涂料占30%,其他整体工业涂料占70%,随着房地产行业的稳定和结构调整, 未来工业涂料比例会继续提高。[图表1-2]
国内涂料行业同质化竞争激烈,产品附加值偏低,产业集中度较低,不利于行业整体良性发展。企业数量方面,据国家统计局统计2017年规模以上企业(年产值2000万元)数量为2057家,不在统计之列的企业是规模以上的数倍(约8000家),这部分企业的主要组成包括小微型企业,散乱污企业, 这些规模以下企业经营环境差, 运营费用低, 技术落后,产品低端,增加了行业的低劣化竞争,让市场混乱,导致涂料行业盈利能力不佳。
据统计,2017年全国涂料前100强企业产量总和占整体48%,相对于14年的41%提升了7%, 2019 年这个比例预计将会达到 51%,可见整体市场在趋于集中化,品牌的规模效应显现,大中型品牌增速较快,通过并购重组或者自我开发,产品线全面发展,中小型品牌产品品类细分化趋势更加明显,定位细分市场,主打核心竞争力。
但是和欧美国家相比,产业集中度还是有较大差距。美国2017年全国涂料产量统计,前10位涂料企业占整个涂料销售产量的75%,相比之下,我国涂料企业仍很分散,国内大型企业规模与一些国际知名涂料企业仍有差距,不利于涂料科技进步和产业发展,使国内涂料企业在国际市场竞争中优势减弱。[图表1-3]
涂料行业的快速发展和当地经济发展有着紧密的联系,我国涂料行业的发展主要集中在华东、华南和华中地区,其总产量基本上可以占到全国的65%左右。相对于的地区来说,华东、华南、华中地区经济发展较快,各种基建机会较多,为涂料行业的发展提供了机会。但是近年来随着产业布局以及环保政策的影响, 涂料区域分布也在发生变化:[图表1-4]
• 华东,华南稳定增长, 西南地区产量增长最快,西南地区受到国家政策的影响(西部开发和一带一路等),多家中外资大型原材料生产商以及涂料生产企业陆续在西南地区投资设厂,开发力度大, 未来涂料增长潜力可观;
• 华北地区受到国家环保安全等政策的影响较大, 从17年开始出现下降, 该地区多家企业受到政策和法规影响, 生产受限,产能转移到安徽, 江西, 西南, 广西等地, 预计未来几年该地区的政策压力有增不减, 对涂料产业升级和低 VOC环保涂料发展有促进作用;
• 在上升的地区中, 有几个省份值得关注安徽,江西,广西,近年来都保持着一定的增长, 这与环保政策推动和产业转入的影响密不可分,从这两年的新建投资工厂的分布来看, 这三个省份的占比较多, 而且以新型环保项目居多;
• 在下降的企业中北京、天津、浙江三个地区较为明显,这与当地环保安全生产政策的落实和执行力度息息相关;
• 保持稳定的省市主要是上海、江苏、广东三个地区, 但是显而易见,未来这三个省市的环保政策压力以及产业转型升级的压力也是日趋严重, 有部分大型企业, 都在积极布局,在西南、华中等地新建工厂,转移阵地;
出现这样的格局一方面与国家产业布局, 固定投资方向有关,另一方面与近年来的环保安全生产政策息息相关, 华北、华东、华南等地的环保压力日益增加, 对涂料生产影响较大。
在过去的一两年中,我国涂料行业经历了历史上极为严峻的考验,一方面上游化工原材料迅猛涨价,给企业造成很大的成本压力,甚至部分企业由于无法将涨价向下游传递而放弃订单;
另一方面严厉的法律法规,越来越严格地规范企业的经营行为,大部分中小企业举步维艰,各地陆续出现涂料企业停产、倒闭现象,促进产业洗牌和升级, 迫使企业在涂料生产的同时,加大了环保和安全生产的投入。但是在环保政策使得中小企业的数量与产能都在减少的同时,大中型企业却供不应求,各大中外资企业相继在全国各地扩建投产或选择OEM代工,市场竞争开始转向良性发展,从而使得行业总体产量呈持续上升态势。
第三方面,近年来,由于供给侧改革、营改增的推进,中国经济发展逐渐放缓,房地产行业不景气,涂料企业的发展道路也越加坎坷。我国涂料正处在油转水的转型升级阶段。
目前我国低端涂料领域将近饱和,而高端涂料大部分市场份额仍被外资品牌所占据,民族涂料企业还未有足够实力竞技高端工业涂料领域。近年来,嘉宝莉、巴德士、三棵树、展辰,晨阳等民族涂料企业纷纷入局工业涂料领域,希望谋求更大的发展空间。不过面对PPG、立邦、阿克苏诺贝尔、关西等跨国大型涂料企业,民族涂料企业的压力不可谓不大。同时,行业还存在众多中小企业,行业集中度较低,不利于企业获得必要的经营利润,在原材料涨价等导致生产成本提高的情况出现时,企业往往只能内部消化。
涂料企业面临着原材料涨价、运输成本上升、能源价格增加、盈利能力下降的困扰。同时,涂料本身并不是最终产品,它要经过涂装变成涂层才能成为最终产品,因此涂料作为“加工服务”型中间行业,上承化工原材料行业,下接涂装和终端市场,其地位相当脆弱,抵御风险的能力也有限,在市场波动以及政策变化时, 一方面大型企业企图收购对手或者同行来减少竞争或者丰富自己的产品线,另外一方面被收购方面对日益增加的压力,也希望得到整合和帮助,从近几年涂料行业的并购来看, 并购重组是未来几年行业结构调整的重要方向,这也是产业整合升级, 提升集中度, 市场有序发展的必然之路。
从产业链的角度看,涂料企业处于中游,下游就是房地产等应用方和终端消费者,而销售是直接或间接通过代理商、渠道商到达用户手中,整个产业链较为分散,上下游割据现象较为严重,协同效应较差。涂料厂家直接参与到终端用户的需求合作中将是一个趋势。当然,战略合作也不仅限于与下游企业,还可以与上游原材料企业,甚至其他跨界合作。涂料企业与上游原材料企业合作可以获得稳定的原料供应和战略支持,与下游企业合作,可以推广产品应用,加强服务,推动创新, 实现共赢。就目前的趋势来看,上下游产业链融合趋势正在逐渐加强。
随着房地产“黄金十年”已经过去,整个涂料行业现在已经进入存量时代。除建筑装饰涂料外, 地坪, 车辆, 轨道交通, 船舶, 工业建筑和厂房等未来的重涂和修补市场潜力巨大,国内的主流涂料企业都在发力重涂市场。相比新建市场,重涂和修补的施工环境和工艺都有很大区别, 这对涂料企业的一体化服务能力提出了更高的要求,因此,以消费者为中心的重涂服务在中国迅速发展。然而,重涂服务在我国发展时间较短,大部分企业发展规划还没有真正落地,也没有建立统一的标准,市场竞争无序,总体上仍然较为混乱,品牌规模效应尚未完全体现。与欧洲发达国家相比澳门第一娱乐娱城官网,中国重涂市场还存在很大的服务缺口。
涂料涂装产生的VOC约占到整个涂料的35%, 其中除去粉末涂料不产生VOC, 建筑涂料的 VOC 含量较少约为2.2%,其他涂料的施工状态 VOC将近56%,其中大部分细分涂料市场没有实行收集处理或者是户外施工无法收集处理。[图表1-5]
从2010年到目前,全国、环保部、国务院、发改委陆续出台多项环保保护以及污染防治和处罚政策。除此之外, 为了积极响应国家政策,各省市也陆续出台了各项环境保护政策,旨在推动产业环保升级,降低VOC,往高固含和水性化等环保化方向发展。[图表1-6]
政策内容更加具体、更加具备操作性,而且为了促进环保涂料涂料产业的发展,对 VOC 的限制是越来越严格。从长期规划,到中期规划,再到短期计划,政策措施越来越清晰。尤其是环境保护税法和十三五挥发性有机物防治方案的出台,给涂料企业切实的压力和动力;
重视发展和推进使用水性,高固含以及粉末、UV等环保涂料和涂装方式。并在十三五涂料发展规划中重点强调发展水性、高固含等配方和涂装技术;
我们认为,政府在推动涂料涂装行业环保化上是不遗余力的,并将不断地推出更多的促进涂料涂装低VOC发展的政策,而未来政策的重点则应放在如何促进政策的落实和执行,以及促进环保涂料的生产和消费(生产澳门第一娱乐娱城官网、使用补贴等方面)。
据统计,截止2018年底,国内有2000多家涂料企业处在“油改水”转型阶段或者在大力研发水性阶段,但是大多数企业和行业只是处在研发阶段,可应用于批量涂装生产的成品为数不多。除建筑装饰涂料外的工业涂料占据整个涂料的70%,约1400万吨澳门第一娱乐娱城官网,其中水性工业涂料的占比约在5-8%,比例很低, 在转水性的道路上, 我国还处于起步阶段。
目前从工业涂料细分行业的水性化进程来看,水性化程度比较明显的几个细分领域分别是:集装箱、大巴、汽车配件、轨道交通、工程机械、钢结构、机械设备等市场。
根据 《十三五:挥发性有机物污染防治工作方案》提出的全面推进集装箱、汽车、木质家具、船舶、工程机械、钢结构、卷材等制造行业工业涂装VOCs 排放控制,我们可以看出到2020年基本要求VOC去除率在50-80%,替代比例根据不同细分行业达到30-100%。[图表1-7]
•目前集装箱行业(干货箱)基本实现全面水性化(车间底漆目前还是溶剂型体系,冷藏箱以及罐式箱等特种箱目前还是溶剂型,但这两方面都已经开始向水性化转变);
•乘用车原厂漆基本水性化(清漆目前还是油性体系);修补漆水性化使用率目前较低,约在3-5%左右,但随着城镇化发展以及政策推动,技术进步, 水性化是大势所趋;汽车金属零部件涂料的水性化发展较快,其流水线的施工工艺和环境适合水性化的转变;
•建筑钢结构涂料由于体量大,分布散乱,不集中, 体系较多且复杂, 目前转水性的进展较慢, 水性化程度不高, 预计到2022年达到10%的转化率;
•工程机械目前主要的水性化来自于三一,雷沃等厂家, 目前水性化比例在10%左右, 在降低 VOC 的方案上有水性、高固含、粉末可选, 三种体系各有千秋,部分厂家选择高固含以及粉末, 部分厂家选择水性, 预计2022年达到30%左右的水性转化率;••目前客车涂料涂装,基本朝着水性化和高固含的路线发展,水性化发展较快,高固含体系在高装饰性要求的场合有用武之地;
•轨道交通方面铁路货车和地铁的水性化较快,动车高铁等随后,铁路货车涂料截止到 19年年底将全部实现水性化,货车和地铁的运营环境相对于动车高铁要简单。随着主机厂的环保压力越来越大,涂料和涂装技术的成熟, 轨道交通的水性化预计在2022年达到86%(铁路货车涂料的体量在所有轨道车型中最大);
•水性是未来重涂和修补市场的主要体系。地坪、车辆、轨道交通、船舶、工业建筑和厂房等未来的重涂和修补市场潜力巨大,国内的主流涂料企业都在发力重涂市场。相比新建市场,重涂和修补的施工环境和工艺都有很大区别,水性将是修补市场的首选。
虽然国家十三五规划是到2020年,但是我们认为水性要得到一个充分的发展,预计还需要5-8年的时间。[图表1-8]
对于原材料商来说,在水性真正转变之前的溶剂型市场可谓是典型的红海,市场同质化严重,低价竞争恶劣,影响整体原材料供应商的营收,同时伴随开工不足,难以发展创新的局面。水性真正伴随着集装箱行业兴起之后,各大原材料商都积极投资投产水性化开发和生产,鉴于目前中国工业涂料水性化程度很低,未来5年内水性带来的发展空间巨大,这对原材料供应商来说是一个值得长期投入和发展的好方向;
对于涂料生产商来说,也是一样,在面临长期的同质化低价竞争以及国家环保安全生产压力的同时,唯有水性化等环保化的路可走,谁走在前面,发展的快,谁的利润和市场份额就能得到保证;我们可以看到一些中小企业由于提前布局,在水性化随着环保政策推动发展起来时,这部分中小企业实现了弯道超车,在水性领域实现快速增长;
另外整个市场的参与者中,除了原材料商和涂料生产厂家,设备制造商也在不断改进和完善水性化的涂装工艺和技术,以满足日益发展的水性化需求;
对于涂料用户来说,目前市场是买方市场,终端用户在面临国家政策导致的降低VOC和安全生产的压力时,可以选择水性,高固含或者其他体系,只要能帮助其降低污染,同时成本最低,就是最好的方案,所以终端用户会把转水性化的压力转嫁给涂料生产厂家和原材料制造商,此二者为了在市场上的生存和发展,会竭力开发新型原料,完善配方技术,简化涂装工艺和降低能耗;
整体来看,根据不同细分市场和涂装环境工艺的不同,水性化、高固含和粉末是发展的三条路线,但综合来看,整个产业链都是联动的,大家都积极参与到水性化的转变中,共同努力共同发展,我们更看好未来水性化的发展。[图表1-9]
来自三方的心声-原材料商、涂料厂家以及终端用户对于当前涂料涂装的水性化、高固含、以及粉末等发展方向的看法
水性更环保,但是水性的生产成本更高,在生产、储存、运输等环节水性的安全性更高。现在防腐涂料主要是两方面,防护和装饰,在装饰的应用上水性还有差距,这也是为什么很多装饰要求高的应用还是用溶剂型或者高固含,例如汽车的清漆;
在客车方面,底漆大部分是电泳,中涂发展水性,面漆往高固含的方向发展,水性在面漆的装饰性和外观方面有差距;
水性发展需要个过程,装饰性要求高的地方需要一个流平的过程。在有强迫干燥的工艺环境下可以考虑发展水性,在常温干燥的地方可以考虑发展高固含体系。另外醇醚类溶剂对有伤害,将来会陆续被禁用;
客车生产过程都是有组织排放,可以倾向于高固体份发展,对于一些无组织排放生产,可以考虑水性体系,溶剂挥发较少;在高表观,高性能场合,水性的应用不太现实。另外水性的废水废渣的回收较溶剂型要难,而且处理成本要高;
现在政府和地方相对于前几年来说,不是一味的要求企业转水性,也开始鼓励企业发展高固含和粉末。对于一些涂装应用,如果是新建的,看企业的选择,可以选择水性也可以选择高固含,都加装回收处理装置。水性带来的二次污染物的回收处理的成本要比溶剂型高,水性的废水和废渣的处理会增加大量含N、O化合物的排放。而且本身水性体系的涂装能耗也要更高;
政府对排放和环保的规划会越来越严格,但是现在高固含体系的施工固含最多也就在75%,将来政策收紧,可能对高固含的发展有影响,对材料提出更高的要求;
RTO,RCO的安装成本,以及后期的运行维护成本很高,倾向于做水性,可以配合活性炭吸附燃烧即可,成本较低;
高固体分体系也是国家政策鼓励的节能减排的优选工艺,高固体分体系特别适用于现有的溶剂型老涂装线的改造,具有投资低、改造时间短、工艺施工窗口宽、能耗低等优点;
国内工程机械的各大主机厂发展情况是大部分企业由于设备和工艺改造的成本太高,所以是往高固含的方向发展,但是对于新建生产线,基本上都是水性体系,一方面响应环保政策,一方面水性线也可以做溶剂型喷涂,总体来看在工程机械行业目前水性和高固含的比例应该在3:7。
总结:当前在水性、高固含以及粉末在涂料涂装环保化的落实过程中各有特色,每种体系都有其在特定市场的应用前景,我们需要理性分析思考,多方共同努力,共同推进涂料涂装的环保化。返回搜狐,查看更多